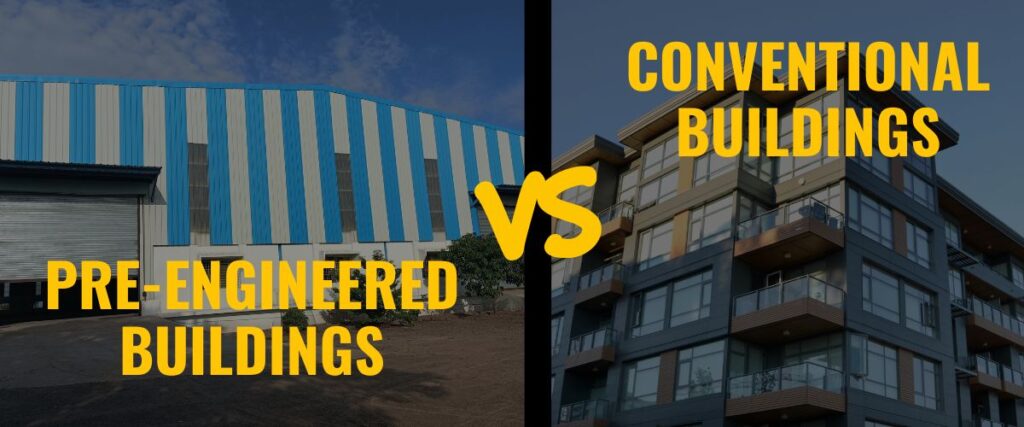
Difference Between Pre-Engineered Buildings and Conventional Buildings
In the realm of construction, it is crucial to understand the fundamental differences between pre-engineered buildings (PEBs) and conventional buildings. Each method possesses unique characteristics and advantages that can significantly impact the construction process, cost, customization, structural integrity, and long-term maintenance. This article aims to shed light on the disparities between pre-engineered buildings and conventional buildings, providing insights for individuals and businesses involved in construction projects.
Design and Engineering
Pre-engineered buildings
Pre-engineered buildings follow a standardized design and engineering approach. They utilize pre-designed components and systems, enabling streamlined design processes. These buildings are engineered for specific loads and structural requirements, employing lightweight materials with high strength-to-weight ratios. The manufacturing process includes rigorous quality control to ensure durability and safety.
Conventional buildings
Conventional buildings, on the other hand, involve customized design and engineering. Each project requires tailored specifications based on unique requirements. This customization adds complexity to the design process, as architects and engineers need to create solutions that meet specific criteria. The materials used and the structural design are project-dependent, requiring careful consideration and analysis.
Construction Process
Pre-engineered buildings
The construction process for pre-engineered buildings is highly efficient. Off-site fabrication and pre-cut components minimize on-site work. The assembly process is quick and straightforward, resulting in reduced construction time and labor costs. These buildings are ideal for projects with tight schedules or budget constraints, as they offer expedited completion.
Conventional buildings
Conventional buildings are constructed on-site using raw materials. The construction process typically follows a sequential approach, where each phase builds upon the previous one. This method requires more time and labor compared to pre-engineered buildings. The sequential nature of construction can lead to longer project durations and increased costs.
Customization and Flexibility
Pre-engineered buildings
While pre-engineered buildings offer cost and time benefits, their design flexibility is limited due to standardized components. Customization is possible within pre-defined parameters, allowing for tailored solutions. However, extensive modifications that deviate from the standardized design can be challenging to implement. Despite this constraint, pre-engineered buildings offer faster project execution and delivery.
Conventional buildings
Conventional buildings provide a high degree of customization and flexibility. Architects and engineers have the freedom to design structures based on specific requirements, allowing for unique architectural features and customized layouts. This versatility is beneficial for projects that demand a more personalized touch. However, the increased customization may lead to longer project timelines and additional costs.
Cost Efficiency
Pre-engineered buildings
One of the significant advantages of pre-engineered buildings is their cost-effectiveness. The use of standardized components, off-site fabrication, and streamlined processes contribute to lower material waste and reduced labor requirements. These factors make pre-engineered buildings an attractive option for projects with budget constraints or time-sensitive schedules.
Conventional buildings
Conventional buildings, with their high level of customization, tend to incur higher overall costs. The need for unique design solutions and the use of various construction materials can escalate material waste and labor expenses. Conventional buildings are more suitable for projects that prioritize distinctive architectural features or design aesthetics, where cost considerations may be of secondary importance.
Structural Strength and Durability
Pre-engineered buildings
Pre-engineered buildings are engineered to meet specific loads and structural requirements. They employ lightweight materials with high strength-to-weight ratios, ensuring structural integrity while minimizing material usage. The manufacturing process adheres to stringent quality control measures, guaranteeing durability and safety
Conventional buildings
The structural design of conventional buildings is tailored to meet project-specific requirements. Architects and engineers carefully select materials based on design specifications and load-bearing considerations. The quality control and durability of conventional buildings depend on the construction practices and the materials chosen, which may vary from project to project.
Long-Term Maintenance and Modifications
Pre-engineered buildings
Pre-engineered buildings require minimal maintenance due to the durable nature of their components. However, their flexibility for major modifications or expansions is limited. These buildings are suitable for applications with stable or predictable future needs, where minimal changes are anticipated over time.
Conventional buildings
Conventional buildings may have higher maintenance requirements depending on the materials and construction techniques used. However, their inherent flexibility allows for easier modifications, renovations, and expansions. This characteristic makes them ideal for applications with evolving needs or potential changes in use over time.
Understanding the differences between pre-engineered buildings and conventional buildings is essential when embarking on construction projects. While pre-engineered buildings offer standardized designs, cost efficiency, and efficient construction processes, conventional buildings provide customization, design flexibility, and adaptability for evolving requirements. Ultimately, the choice between the two methods depends on project-specific factors, including budget, timeline, design preferences, and long-term goals. By carefully evaluating these considerations, individuals and businesses can make informed decisions to achieve successful construction outcomes.